Guide to composites
What are composites?
Composites, also known as fiber-reinforced plastics (FRP), are synthetic materials comprised of reinforcements (fibers) and a matrix (resin). On their own, these materials only provide limited use, however combined into a composite the new material provides many useful advantages.
In composites the reinforcing fibers are used to resist tensile and compressive loads, while the matrix (the “plastic”) transfers the shear.
In today’s industrial composites the two most commonly found reinforcements are glass fiber and carbon fiber. There are many other fibers that may be used, fiber selection largely depends on the material properties required and the manufacturing techniques involved.
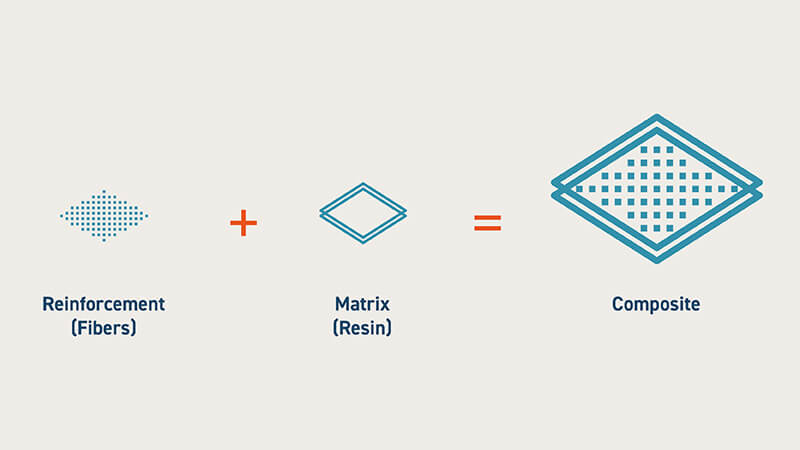
Advantages of composites
Composites provide many advantages, both in the ability to tailor the composite’s fiber and resin chemistry and composition as well as the weight savings and long-life attributes compared to other materials like steel and aluminum.
Light weight load bearing characteristics combined with required stiffness and strength are easily achieved with composites. Additionally, composites are very durable materials resistant to many of the ambient environmental conditions composites may find themselves used in. These include:
Lightweight
Composites typically have a specific gravity one-quarter that of steel and two-thirds that of aluminum, this helps save weight in a wide range of applications without sacrificing strength or stiffness.
High strength and stiffness
Composites have a higher strength-to-weight ratio compared to steel or aluminum, and stiffness properties which outperform plastic and other non-metallic materials.
Cost-efficient
Composites are shape and specification ready. That means that unlike metal fabrication, no cutting, welding or grinding is required.
Thermally efficient
Fiberglass is an excellent insulator and does not conduct heat or cold, helping improve the thermal efficiency in applications where it is used (especially in applications like window and door frames).
Chemical and corrosion resistance
Composits offer long-lasting resistance to acidic, salty, or alkaline conditions. This makes them exceptionally suitable for harsh environments like water treatment facilities, downhole oil & gas application, or even at the sea shore.
Design flexibility
Composite design takes advantage of both being able to combine multiple functions into a single profile, with the choice of fibers, matting, and resin systems to meet a broad spectrum of challenges and requirements.
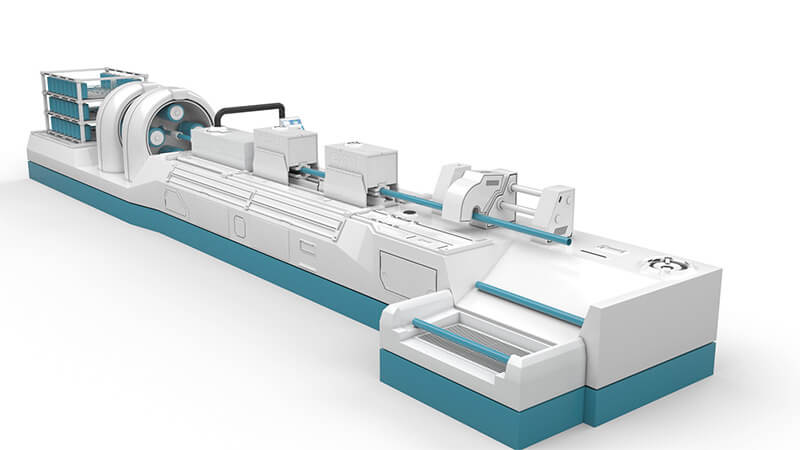
How are composites manufactured?
There are many methods used to manufacture composite materials. At Exel, we specialize in pultrusion, pull-winding, and continuous lamination. However other methods commonly used include pre-preg molding, resin transfer molding (RTM), filament winding, injection molding, and of course hand-layups. Each of these methods offers different production advantages and their use is dependent on many factors, including volumes of production and the geometry of the manufactured profile.
Continuous lamination, pultrusion, and pull-winding manufacturing are continuous processes where the manufactured profile is output as one single product which is then cut (flying shear) to desired lengths at the end of the manufacturing process. We have developed several decades of expertise in these processes and are always thinking how to improve them for our customers.
What are thermoset and thermoplastic composites?
There are two major types of resin used in the production of composites; thermosetting and thermoplastic. Thermosetting resins are currently the most common, but as composite use expands, thermoplastic resins are increasingly being explored.
Thermosetting resins are hardened via curing, using heat, to form heavily cross-linked polymers with insoluble or infusible rigid bonds that will not melt on exposure to heat. On the other hand, thermoplastics are branches or chains of monomers that soften when heated and solidify once cooled, a reversible process with no chemical bonding. Put simply, you can re-melt and re-form a thermoplastic, but not a thermoset.
Guide to composite raw ingredients
Composites, also known as fiber reinforced plastics, are generally produced by combining a reinforcement and a matrix. The most common reinforcements are glass and carbon fibers. The matrix, commonly referred to as a resin, includes a wide range of types, each with a unique chemistry yielding different mechanical properties in the final composite product.